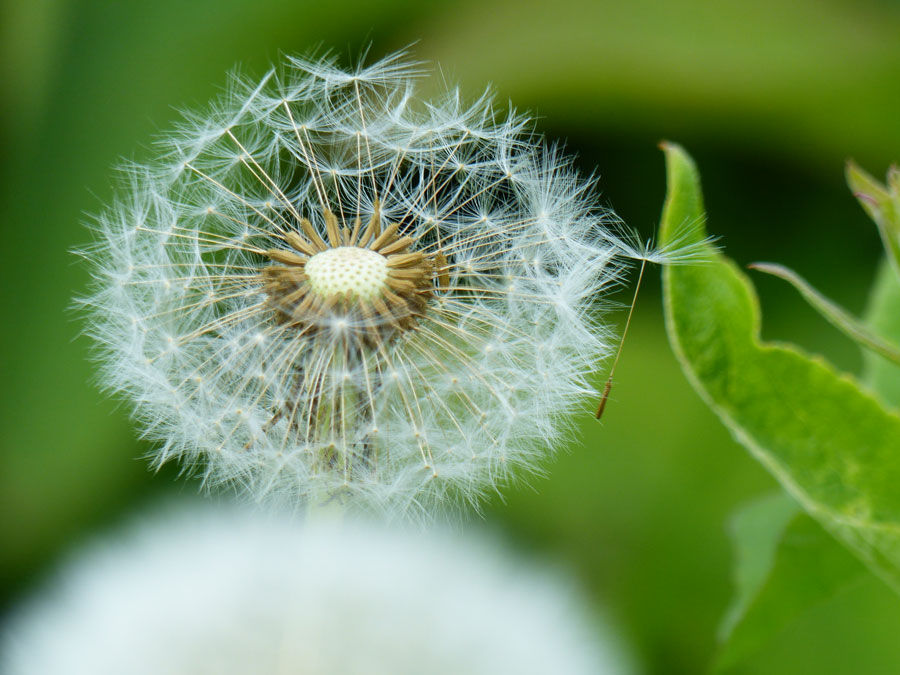
Business advice
Lundy Island
The traditional waste management practise on Lundy, as with so many other islands, was simple - first burn it and then tip the non-combustibles off the cliff. So, in 2000, with Lundy now designated a marine reserve, and with greater enlightenment, (not to mention legal constraints!) it was decided to explore alternatives. The first solutions still relied heavily on transporting all the 'waste' off the island.
Wheeled bins and skips were trialled, but wheelie bins did not work well on the rough terrain and the 8 cubic yard skips, which had been used previously with mixed waste were too heavy when filled with separated putrescible waste or glass, to be lifted on the ship. Smaller skips were then used, but bad weather means that the ship could not always dock and stinking skipfulls would accumulate. The island's passenger and supply ship MS Oldenburg can bring 250 tourists a time and sharing the deck with a smelly skip is not a desirable part of the tourist day trip!
In 2002 a grant was received from Pennon (whose two main subsidiaries are South-West Water and Viridor Waste Ltd) and a team of students from Exeter University undertook a waste management audit. This led to the introduction of a compactor and the separation of the dry recyclables but they were still left with the biggest problem - the smelly stuff!
In January 2004 I showed Paul Roberts, the manager of Lundy Island, around the Proper Job demonstration site in Chagford. He was desperate for a solution to several 'waste' problems on the island. I recommended that a 'Rocket' be used, also that a cardboard shredder would be useful as a mix for the kitchen waste along with any tougher woody shreddings etc. Five to eight tonnes of packaging are generated on the island each year and that could be used as bedding, before being mixed with the kitchen waste, also saving bringing so much straw onto the island.
While Paul was at Proper Job, we also talked about ways to compost the sewage and how to transform the waste cooking oil into fuel - he left reeling with his head full of new ideas. I was delighted to find that by the end of the year that the building that houses the compactor also now has a 'Rocket', and a proper separation area for all the recyclables.
Before Paul left he told us that Lundy is a part of a small islands network. They meet up and exchange ideas and best practises, so I really hope that these ideas will spread world-wide - and who know, from there start to creep onto the mainland!
Wetherby Young Offenders
During the Compost Doctors project, we had the opportunity to help the prison improve its food waste composting system. They already had a small rather elderly 'Big Hanna' composter which was designed for a much smaller throughput. Steve Ross-Smith and Nicky, who together designed and built the Scotty HotBoxes, installed several to add capacity to the Big Hanna so that they did not have to purchase a bigger machine. When we visited the manager of the system was extremely enthusiastic about the Scotty HotBoxes and showed us how they were steaming away and continuing the composting process.The Big Hanna mixes the food waste with woodchip and other 'soak' materials and the composting process is accelerated through the turning cycle. These composters are designed to produce mature compost but that means buying an expensive machine to deal with larger throughputs. Why not buy a much smaller machine instead and increase capacity using the Scotty's HotBoxes?
Unfortunately I was not allowed to take and photos in the prison to record the system.
​
​